Melting & Pouring
Our process line is equipped with advanced machinery designed to optimize the melting and pouring operations. This setup ensures a smooth and efficient workflow, crucial for producing high-quality iron castings
In the melting process, the chosen iron ore, along with any additional elements required to create the alloy, is heated to a controlled temperature. This precise control is vital to achieve the right composition and consistency of the molten metal.
Once the metal reaches its molten state, it is carefully poured into the pre-designed mould to form the final product. The accuracy of this pouring stage plays a key role in ensuring the casting’s quality and structural integrity.
At Veejei, we place great emphasis on testing at both the melting and pouring stages. These critical checkpoints help us maintain the effectiveness of the process, directly influencing the quality and performance of our iron castings.
Inductotherm Make : Duraline Furnace
- 1000 Kgs – 1 No & 2000 Kgs – 1 No
- 3000KW/500 Hz VIP-I Series IGBT Dual Mode-R-LI Inverters of 1500KW & Converter of 3000KW 12 PHASE- 24 PULSE
- I-Optimizer Plus – 1 No
Capacity to Produce
- 30 Kgs to 250 Kgs (single unit) in all Grades.
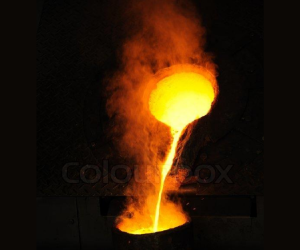
During the pouring process, the molten metal undergoes a crucial step known as inoculation. This process plays an essential role in counteracting shrinkage defects that may occur during solidification, thus improving the overall quality and properties of the castings.
Inoculation ensures that the metal achieves the desired microstructure, enhancing its strength and durability. By carefully controlling this step, we can produce castings with superior mechanical properties that meet stringent performance requirements.
Following inoculation, regular and essential quality tests are conducted on the material. These tests focus on evaluating key factors such as nodularity, temperature, and chemical composition. Each of these parameters is carefully monitored to ensure the final product meets the highest standards.
By performing these quality checks, we ensure that the castings not only meet customer specifications but also adhere to industry standards for reliability and performance.
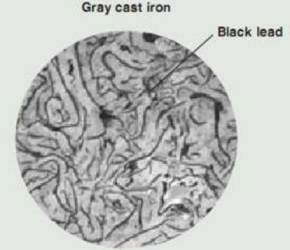
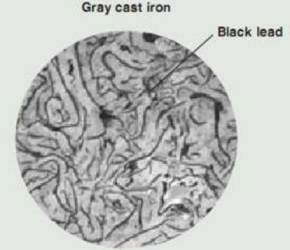
We are equipped and experienced to produce any Special grades as per Customer expectations or International Standard Specifications like IS, ASTM, SAE, DIN, EN, and JIS. We handle regularly are mentioned as follows,
Manufacturing and Supply of Machined & Un machined SG, Grey Iron Castings.
S.G Iron Castings
- 400/12, 400/15, 400/18, 450/10, 500/7, 600/3, 600/10, 650/5 and 700/2.
Grey Iron Castings
- FG150, FG220, FG260, FG300